How Diamond Blades Work
Diamond blades contain industrial-grade diamonds in segments or rims on their cutting edge. As the blade is used, the abrasive qualities of the material being cut (such as concrete) wears down the segment. Diamond crystals either get crushed or let loose as the metal matrix gets worn away, exposing new diamonds to continue the cutting.
The abrasive quality of the material being cut is a large factor in choosing the correct blade for a job. Harder materials, such as cured concrete, require a blade with a softer metal mix. This softer mix will ensure adequate erosion of the segment bringing new diamond to the surface at the optimum rate.
Soft materials such as green concrete and asphalt tend to wear down segments faster. Therefore, segments with a harder, more wear-resistant metal mix in the segment, provide longer blade life and overall better performance.
Abrasive materials tend to erode the metal core, or center, of diamond blades causing undercutting. Undercutting is usually concentrated on part of the core that attaches to the segment. If undercutting is excessive, it can cause segment loss and damage the blade. Coast To Coast Supply offers 3 types of undercut protection which reduce abrasive slurry accumulation beneath the segments to provide extended blade life.
Segments come in different heights. The total segment height is not as important and the diamond depth – the portion of the segment that contains diamonds. The diamond depth combined with diamond concentration and quality determines the overall performance value of the blade.
The accompanying chart shows the effect different variables have on a diamond blade cutting speed and blade life.
Understanding The Aggregates
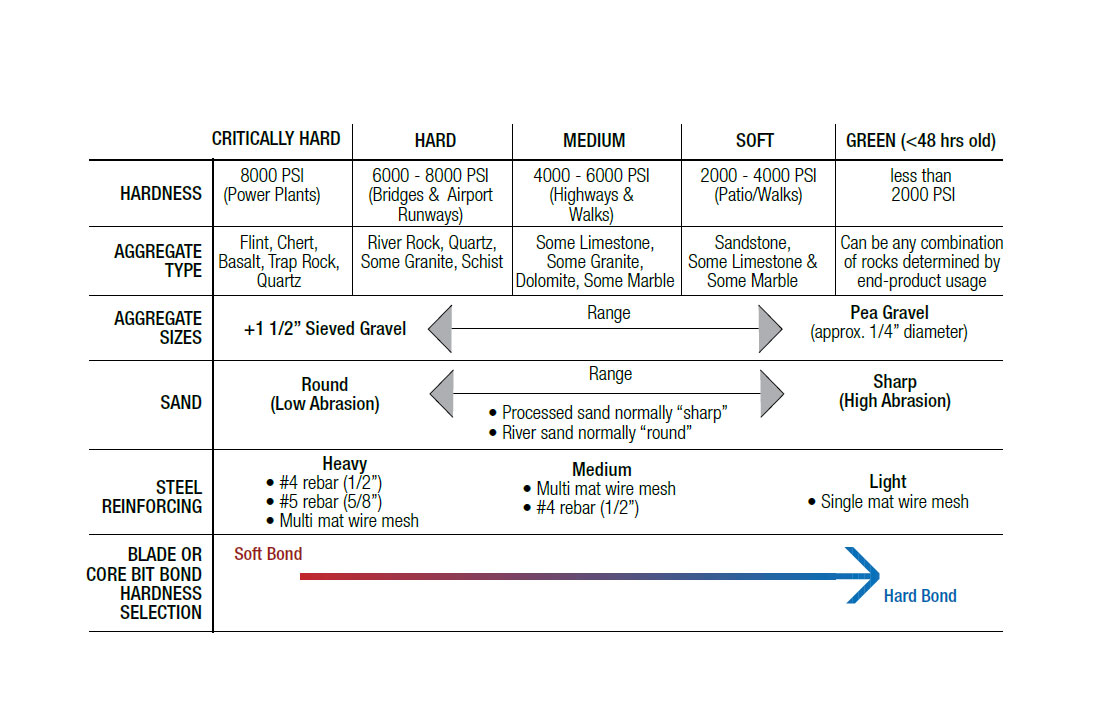
Aggregate Map
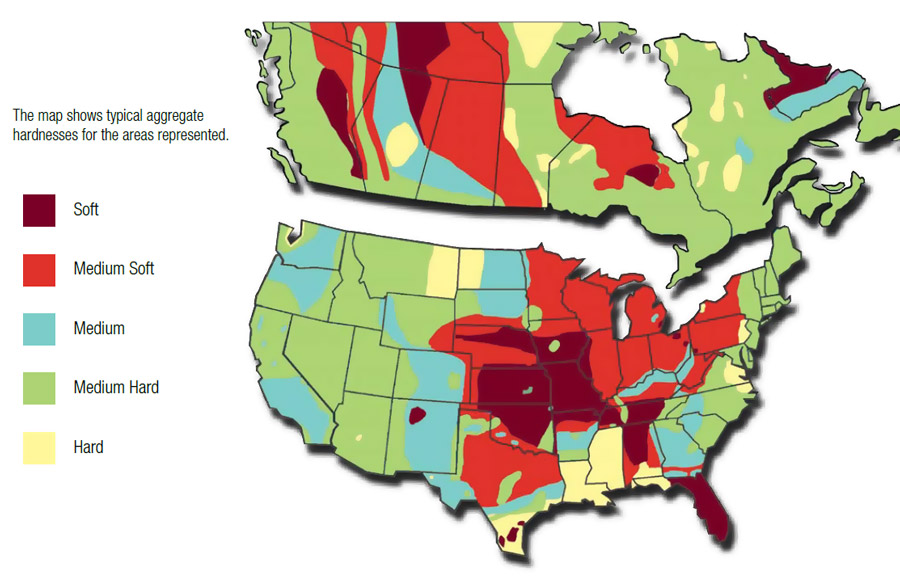
Cutting Depth Speed Chart

Blade Troubleshooting
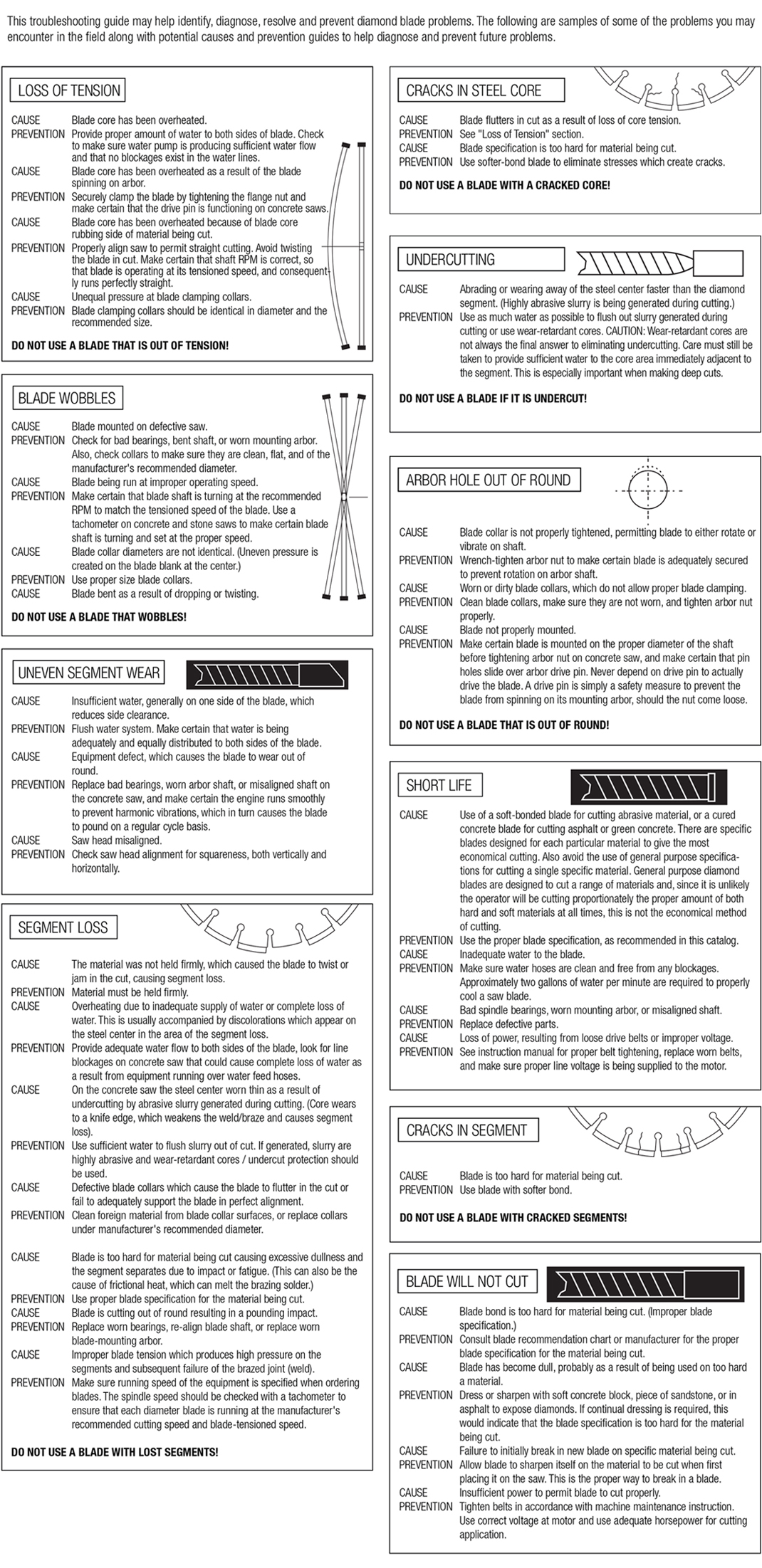